Water-borne PU Dispersions for Direct-To-Metal Coatings: Barrier Properties and Corrosion Resistance
- Team C&E
- Mar 2, 2022
- 2 min read
Updated: Mar 3, 2022
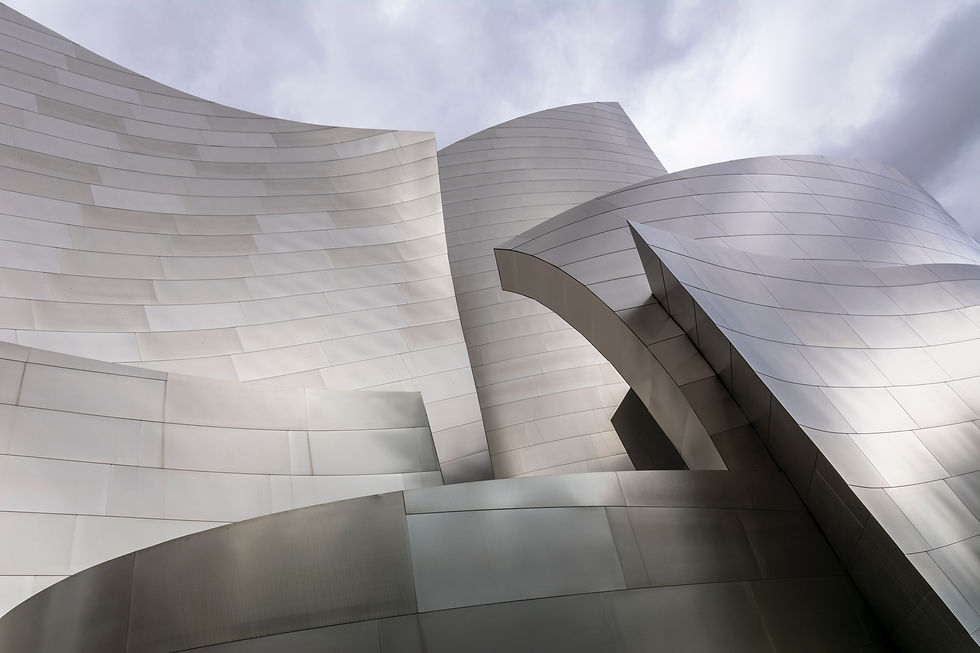
The process in which metals and other materials are gradually destructed by electrochemical reactions with the environment they exist in is known as corrosion. The consequences of metal corrosion are vast and may lead to major accidents and loss of valuable products. Application of coatings is one of the most widely utilized methods of corrosion protection, as it is economical and can be applied easily.
When compared to other water-borne polymers, polyurethane (PU) is preferred for coatings as it has numerous favourable properties. Polyurethane Dispersions (PUDs) have many applications in various industries due to their resistance to chemicals, corrosion and abrasions, excellent adhesion to many different surfaces and durability. These coatings can however be harmful to the environment when they consist of harmful solvents and other toxic compounds. Many of the corrosion-resistant coatings are solvent-borne, but because of the high content of volatile organic compounds (VOCs) emitted by them, they are not preferred. Currently, water-borne anti-corrosion coatings have gained a lot of attention for the protection of metals as they keep the emission of VOCs to a minimum. As they are more eco-friendly, they are being studied as a replacement for other solvent-borne coatings.
The stability and strength of the metal when it is exposed to aggressive media depend on the protective factors of surface coatings which are formed. The potential of the film formed to act as a corrosion barrier depends on adherence, conductivity, morphological properties, chemical composition, solubility and hygroscopicity.
Two important coating technologies, epoxy and PU systems are known for their ability to protect the base material. Epoxies show good adhesion to metals and provide resistance to high impact, chemicals and moisture. However, they are inflexible, form chalky films when exposed to harsh environments and can cause cracking when used in heavy-impact applications. They cause yellowing when exposed to UV radiation and become brittle at lower temperatures. PU coatings are therefore preferred in metals to control corrosion as they are highly flexible and have suitable adhesion properties. When used for metal coatings, PUs form a glossy, thin film which has good performance towards weathering. These durable coatings are highly resistant to corrosion, chemicals and abrasions. Rigid direct-to-metal (DTM) PU coating systems are utilized in applications involving steel storage tanks and pipe coatings.

Solvent-based PUDs and high solid two-component urethanes are however preferred for metal (steel and direct-to-metal) coatings, as they provide stronger barrier properties. High solid systems also provide thicker film build and decreased shrinkage. Despite the various advantages of water-based coatings, their anticorrosion properties are mediocre compared to solvent-borne coatings. This is due to retention of hydrophilic groups during the process of film formation, which reduces the ability of the shield to resist moisture and diffuse vapours. Hence, corrosion fillers or inhibitors (inorganic nano/micro particles) must be added to enhance the corrosion resistance of water-borne coatings. There is still room for improvement regarding barrier properties and electrochemical impedance of water-borne PUDs to reach the level of performance of solvent-borne anti-corrosion coatings.
More information about C&E’s eco-friendly ‘Puthane’ range of water-borne PU coating products can be found on our website.
By Ashni Arun on March 2nd, 2022
コメント